
New Methods for Activated Carbon Decolorization in Stevia Extraction
In the extraction and purification process of steviol glycosides has several steps which involve removal of coloured components from liquid extract by activated carbon. Activated carbon treatment is a very delicate unit process which needs proper equipment and precision process control. The conventional Chinese origine extraction process engineering is yet to assimilate the modern methods of activated carbon treatment. Thus, very often the extraction units end up with activated carbon treatment units with primitive design with very low efficiency and high process time.
Let us discuss about some modern activated carbon treatment systems and equipments which may be integrated into the extraction process for higher process efficiency and lower processing cost.
Activated carbon, also called activated charcoal, or activated coal, is a form of carbon processed to have small, low-volume pores that increase the surface area available for adsorption or chemical reactions.
Due to its high degree of microporosity, just one gram of activated carbon has a surface area in excess of 500 m2 (5,400 sq ft). Activated carbon binds large organic molecules on its surface by a physical process called adsorption. The adsorption capacity of a specific substance on activated carbon surface is dependant on the concentration of substance in the extract, the temperature and the polarity of the substance. A polar substance (= a substance which is highly soluble in water) cannot or is badly adsorped by active carbon, whereas a non-polar substance can be removed totally.
The materials which imparts colour to the extract during stevia extraction process are -
-
Plant pigments, carotenoids, chlorophyll and its degradation products.
-
Tannins, phenolics and poly-aromatics
-
Products formed due to Maillard reaction between sugar and amino acids
-
Enzymatic auto-oxidation products
All this colour contributing substances are effectively removed by Activated Carbon treatment. Activated carbon treatment is generally adopted in the following processes.
-
Decolourization of alcohol eluted steviol glycosides before ion exchange
-
Decolourization of vacuum evaporated and concentrated steviol glycoside syrup before spray drying
-
Decolourization of vacuum evaporated and concentrated Rebaudioside A syrup before spray drying
Activated carbon process in conventional Chinese technology
In this technology, the decolourization by activated carbon is done by the following process.
-
The extract with coloured contaminants are taken in a large vessel provided with slow speed agitators.
-
Measured amount of finely devided activated carbon is then added to the liquid and mixed with the help of the agitators.
-
The activated carbon particles are kept in suspension in the liquid with continuous agitation until desired degree of decolourization is attained.
-
Then the liquid is discharged into a smaller agitated vessel. The liquid is then pumped under high pressure to a plate and frame filter press to filter out the carbon particles. The filtration is done under a stable pressure. The filter press is provided with a return line, so that a part of the filter cake is washed back in the small agitated vessel.
-
The filtrate is stored in another tank and sent for further processing.

The drawbacks of this method are –
-
This is a batch process and not compatible with a continuous process line
-
Number of equipment and vessels required is high
-
A lot of manual intervention is required
-
Cumbersome cleaning of equipments and poor process hygiene
-
Poor process control
-
Higher energy requirement (Two agitators, three pumps, hydraulic drive for the filter press)
Steviol Glycoside Loss During Activated Carbon Treatment
Activated carbon also adsorbs some amounts of steviol glycoside, and thus, optimization of quantity of activated carbon is very important to achieve desired decolorization effect without significant loss of steviol glycoside. Ding et al (2013) reported the optimal process parameters for activated carbon treatment. According to this report, the optimum process parameters are - Activated carbon proportion 1%, Process temperature 10℃, Reaction time 0.5h and the pH value of 7.0. With these process parameters the steviol glycoside loss through adsorption on activated carbon was 2.72%.
Ding Hong-Mei, Tian Hong ,Lian Yun-He and Niu Zhi-Ping (2013) : Study on bleaching effect of activated carbon on stevia solution, China Food Additives : 2013-04
Alternative Methods
Packed bed filter process
To make the activated carbon treatment process compatible with a continuous process system, the alternative method may be use of a flow through packed bed column, filled with granular activated carbon. This method may make the unit process much simple with lesser number of vessels, pumps and moving parts.
In this process, the extract is slowly passed through a packed bed of activated carbon packed in a column. As the extract passes through the column, the coloured impurities, oily materials and large non-polar organic molecules are adsorbed by the carbon and retained in the bed. After a certain time, the activated carbon in the column is taken out and replaced with a fresh batch.

Industrial Activated Carbon Filter Equipment

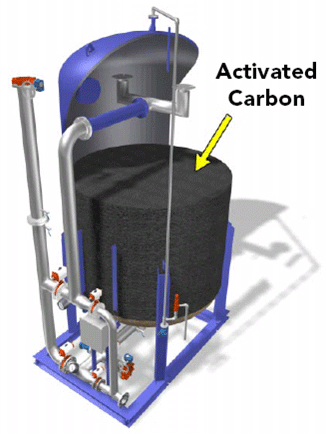
Cut-away view of an Industrial Activated Carbon Filter
Activated carbon filters can be constructed as both down-flow type (crude extract fed on the top of the bed and de-colourized liquid comes out from the bottom) or up-flow type (crude extract fed from the bottom of the bed and it flows up through the bed and it is discharged from the top of the bed).
The Major advantages for the process are –
-
Less equipment and less floor space
-
Continuous operation with better process hygiene
-
Less manpower requirement
-
Lower carbon dosage
This process has also a major drawback. After the carbon gets saturated and looses it adsorption capacity, it needs to be discharged from the column and replaced with a fresh batch. The changing of the carbon may require significant down time. To take care of this, several activated carbon columns are connected in parallel and the column requiring carbon change are shut off, keeping the other columns operational. In a system like this, the system never needs complete shut off.
Different Forms of activated carbon used in packed bed carbon filters

Granular Activated Carbon
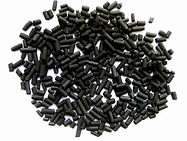
Activated Carbon Extruded Pellets

Activated Carbon Honeycomb Blocks

Engineering details of a mid-sized packed bed activated carbon filter
Pulsed Bed Activated Carbon Process
The Pulsed bed system is a modification of the Packed Bed System. The system comprises of a tall column filled with activated carbon on a supporting mesh. The column has provision of periodic addition of fresh or regenerated activated carbon at the top of the column. It has also provision for a bottom hatch for discharging spent activated carbon at the bottom of the column.
In this system, the crude extract is introduced into the column through a distribution manifold at the bottom of the column. The extract slowly flows upwards through the carbon bed and decolorized extract flows out through a collector near the top of the column.
In the packed bed, Activated carbon which has completely lost it’s decolorizing ability (spent carbon) lies on the bottom of the bed and a is removed periodically. Simultaneously, the same quantity of regenerated carbon is fed to the column from the top (Pulse operation). Thus, the bed ends up having stratified layers of activated carbon – with the layer having activated carbon with least adsorption power at the bottom and the freshest activated carbon with highest adsorption power at the top of the bed. The incoming crude extract is first exposed to the activated carbon with least adsorption power and after that, gradually, the extract is exposed to activated carbon with more and more adsorption power. Hence, the interaction between the crude extract and activated carbon almost becomes counter current.


Rotating Packed Bed Reactor System
Concept of a rotating packed bed (RPB) as a mass transfer equipment was developed by Ramshaw and Mallinson in 1979 (Ramshaw C and Mallinson R : Mass Transfer Process; European Patent 2568B, 1079 US Patent 4263255, 1981). A RPB works on the principle that the gravitation flow of fluid through a packed bed is replaced by a centrifugal field, which could be even 1000 times stronger than the gravitational field. This technology is named as HIGEE, an acronym for high gravity. A doughnut shaped bed is spun at high speed to achieve this centrifugal force in a RPB. Initially the RPB-HIGEE systems were used in separation processes such as distillation and absorption, however, it can also be applied in mass transfer limited reacting systems.
Traditionally the fixed bed systems are used to treat crude extract by adsorption. In this case, the gravitational force is responsible for the flow of liquid through the bed, which often suffers from clogging and decline in throughput. Additionally, the problem of channel formation inside the column and fouling hinder the proper utilization of the total adsorption bed. The poor mass transfer efficiency and large size of the columns make these conventional processes expensive and difficult to handle. Advantages of using high gravimetric systems are higher throughput, formation of thinner liquid film over the packing resulting in decreased external mass transfer resistance, use of higher surface packing per unit volume of packed bed, better distribution of liquid over the packing and lower static holdup. This would aid in reducing the size of the processing equipment significantly in comparison to a conventional packed bed and is therefore, likely to reduce the overall cost of activated carbon treatment.
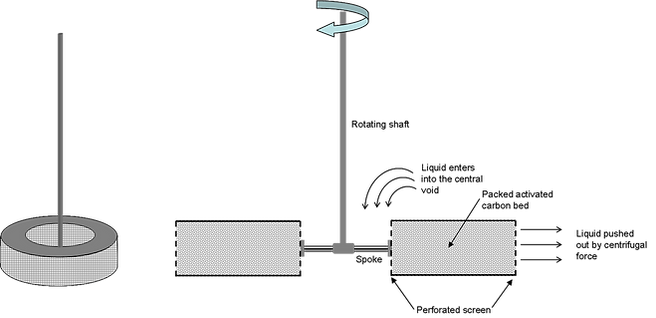
Rotating Packed Bed Reactor
Conventional stirred tank reactor
Comparison of decolorization speed in Rotating Packed Bed reactor and Conventional stirred tank reactor
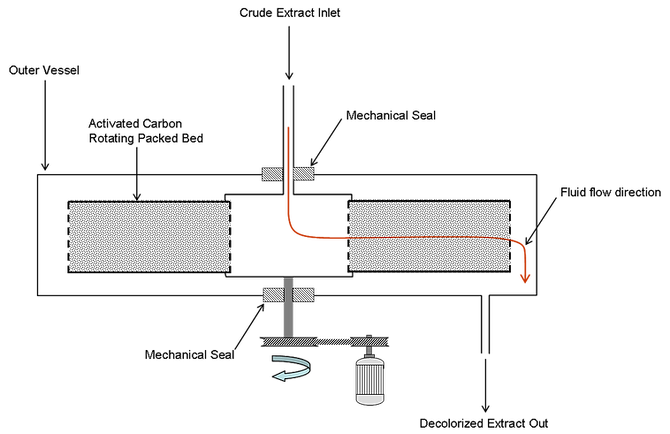
Industrial Rotary Packed Bed Carbon Filter – Simplified Schematic